From 1 April 2025, all tipping body fitments must comply with the VSB6 J4 Tipper Code, marking the final phase of the National Heavy Vehicle Regulator (NHVR) compliance transition.
For tipper body manufacturers and Approved Vehicle Examiners (AVEs), this means ensuring that all designs meet the new structural assessment standards without unnecessary disruption to existing workflows.
The challenge for the industry is twofold:
- Manufacturers must navigate the engineering and certification process efficiently, ensuring compliance while minimising impact on existing designs and production timelines.
- AVEs and other approved engineering signatories need to ensure they are assessing and certifying vehicles accurately under J4, while managing increasing certification demands.
That’s Where Smedley’s Engineers Come In
As one of the only firms offering a full suite of engineering services tailored to the heavy vehicle industry, Smedley’s Engineers provides an end-to-end compliance solution, covering structural analysis, design assessments, and certification-ready documentation.
Most importantly, our expert team ensures compliance is achieved with minimal modifications to existing designs, helping:
✔ Manufacturers avoid costly rework and disruptions to production.
✔ AVEs and other approved engineering signatories access reliable and accurate compliance documentation to facilitate certification.
This guide will cover:
- What the VSB6 J4 Tipper Code entails and key compliance deadlines.
- Common challenges for tipper body manufacturers and AVEs—and how to overcome them.
- How Smedley’s Engineers streamlines the compliance process to keep businesses moving forward.
By the end, you will have a clear compliance roadmap and the confidence to navigate J4 certification without unnecessary headaches or disruptions.
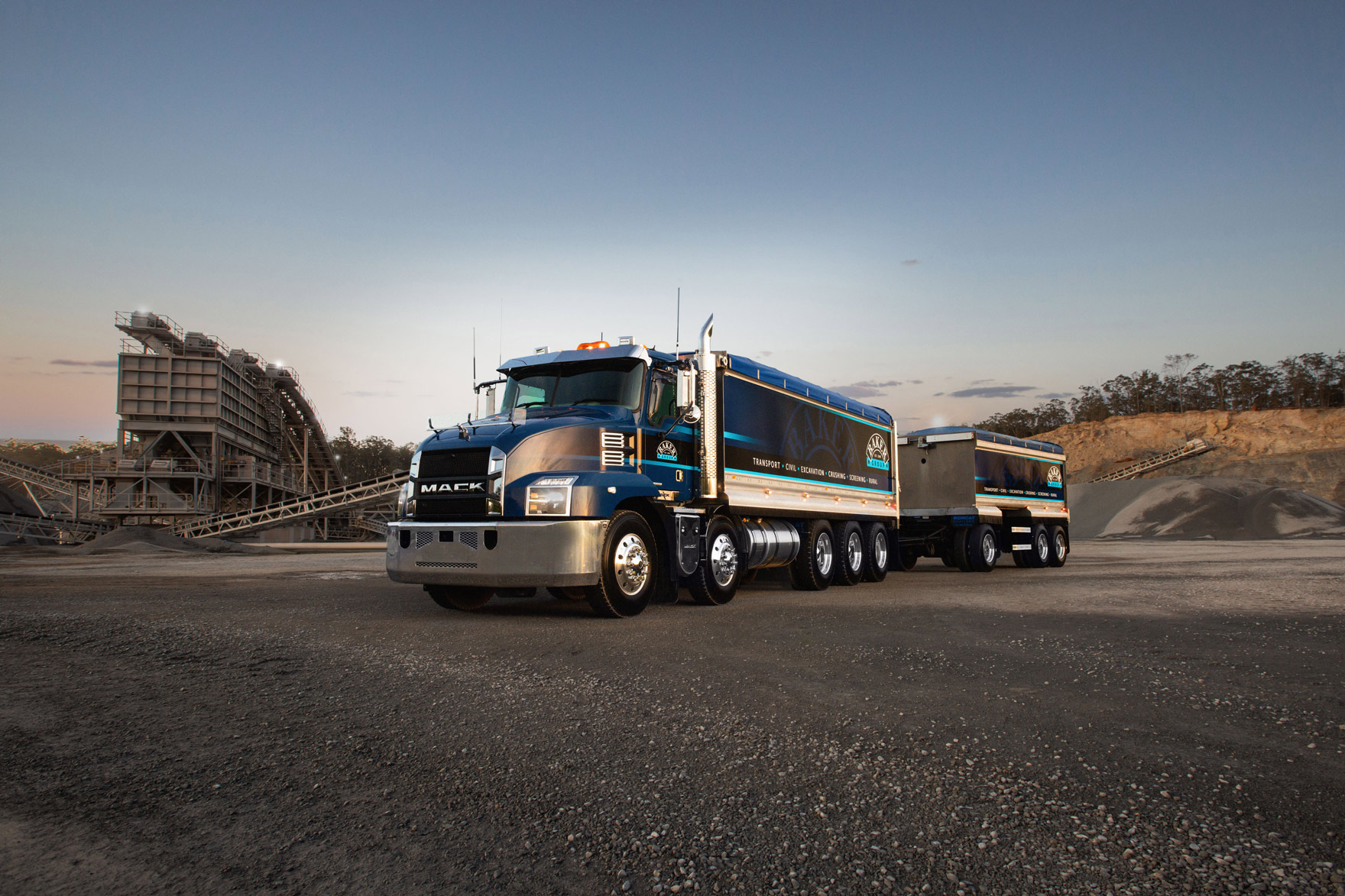
Borcat – Bakers Anthem
Understanding the VSB6 J4 Tipper Code
As part of the NHVR updates to VSB6, the J4 Tipper Code introduces new compliance requirements for tipper body fitments. These changes are designed to improve safety, standardisation, and structural integrity across the heavy vehicle industry.
For manufacturers and tipper builders, this means ensuring that all designs are assessed and certified under the J4 framework within the prescribed timelines.
For AVEs, it requires a thorough understanding of the updated structural assessment criteria to accurately evaluate and certify compliance.

Borcat Rigid Truck
Key Compliance Deadlines
The transition to J4 compliance is already underway, following a structured timeline:
- 1 July 2024 – The revised VSB6 J4 Code was published on the NHVR website, allowing AVEs and bodybuilders to review the new standards and begin preparing for accreditation.
- 1 October 2024 – The six-month transition period commenced. Tipper manufacturers who have not yet transitioned to a J4-compliant design should now be submitting their designs for assessment by an AVE to avoid last-minute delays.
- 1 April 2025 – The final implementation phase takes effect. From this date, all tipping body fitments certified under the J1 code must be transitioned to an approved J4 design. There are no extensions or exemptions—compliance is mandatory for all.
With the deadline fast approaching, manufacturers must act now to ensure their designs meet J4 requirements before enforcement begins.
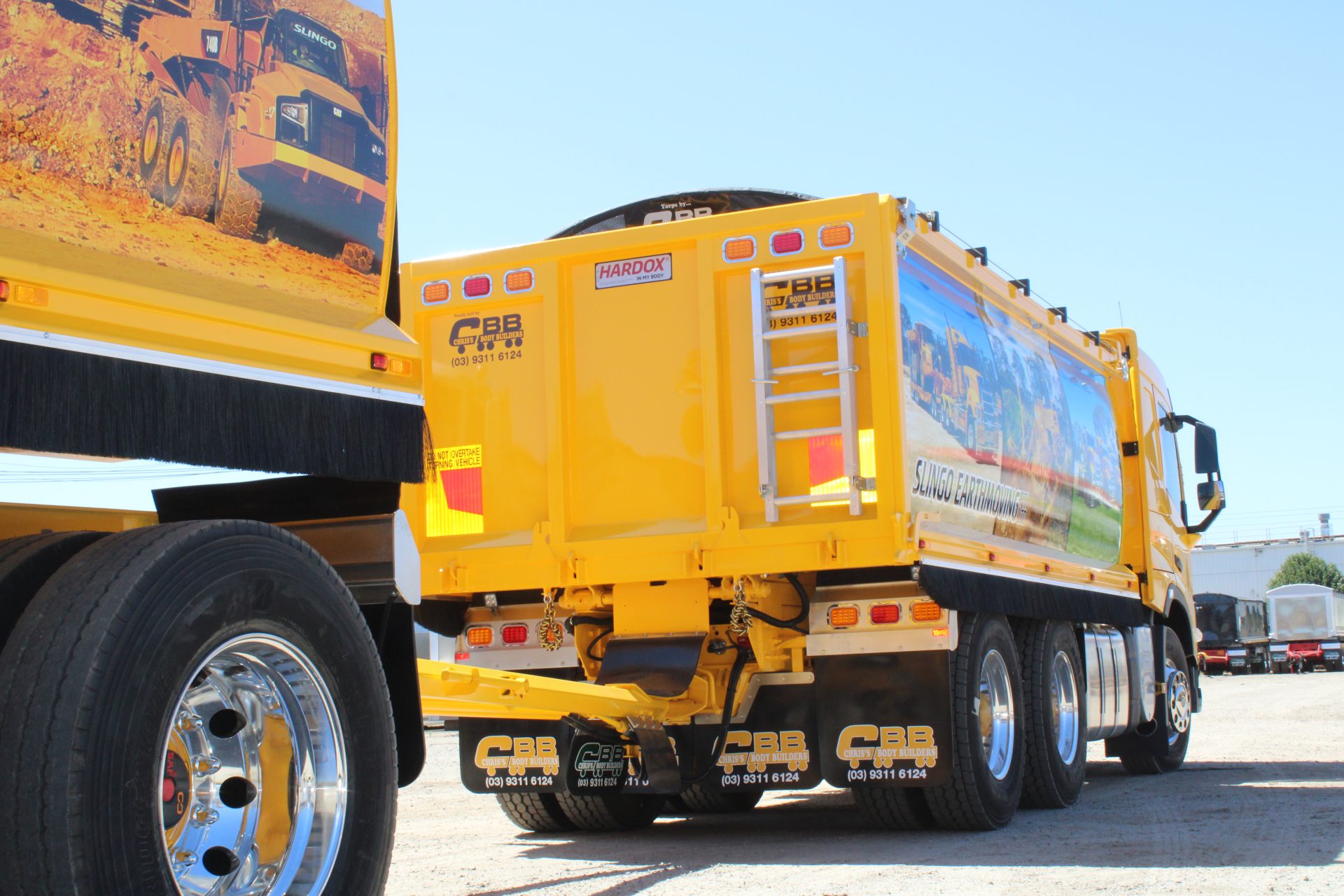
Chris’s Body Builders
Why Is This Change Happening?
The introduction of the J4 Tipper Code ensures that tipper body fitments meet modern safety, durability, and operational standards. The NHVR has identified key structural and functional areas requiring updates to enhance vehicle integrity, reliability, and safety compliance. These updates focus on:
- Tipper hinge – ensuring durability and proper alignment with compliance requirements.
- Subframes and mounting to chassis – strengthening structural connections to prevent failures.
- Tailgate design and grain doors – improving safety and functionality for different load types.
- Hoist cross members – reinforcing lifting points for greater stability and durability.
- Pneumatic and hydraulic layout – ensuring safe and efficient operation of tipper mechanisms.
- Tipper control and warning systems – enhancing operator awareness and preventing misuse.
For manufacturers, this change means adapting to new compliance methods while maintaining operational efficiency. The key challenge is ensuring that existing designs remain viable with minimal modifications, avoiding costly redesigns and disruptions to production.
For AVEs, the update introduces stricter assessment requirements, meaning examiners must carefully evaluate tipper body structures and operational components to ensure full compliance before certification.
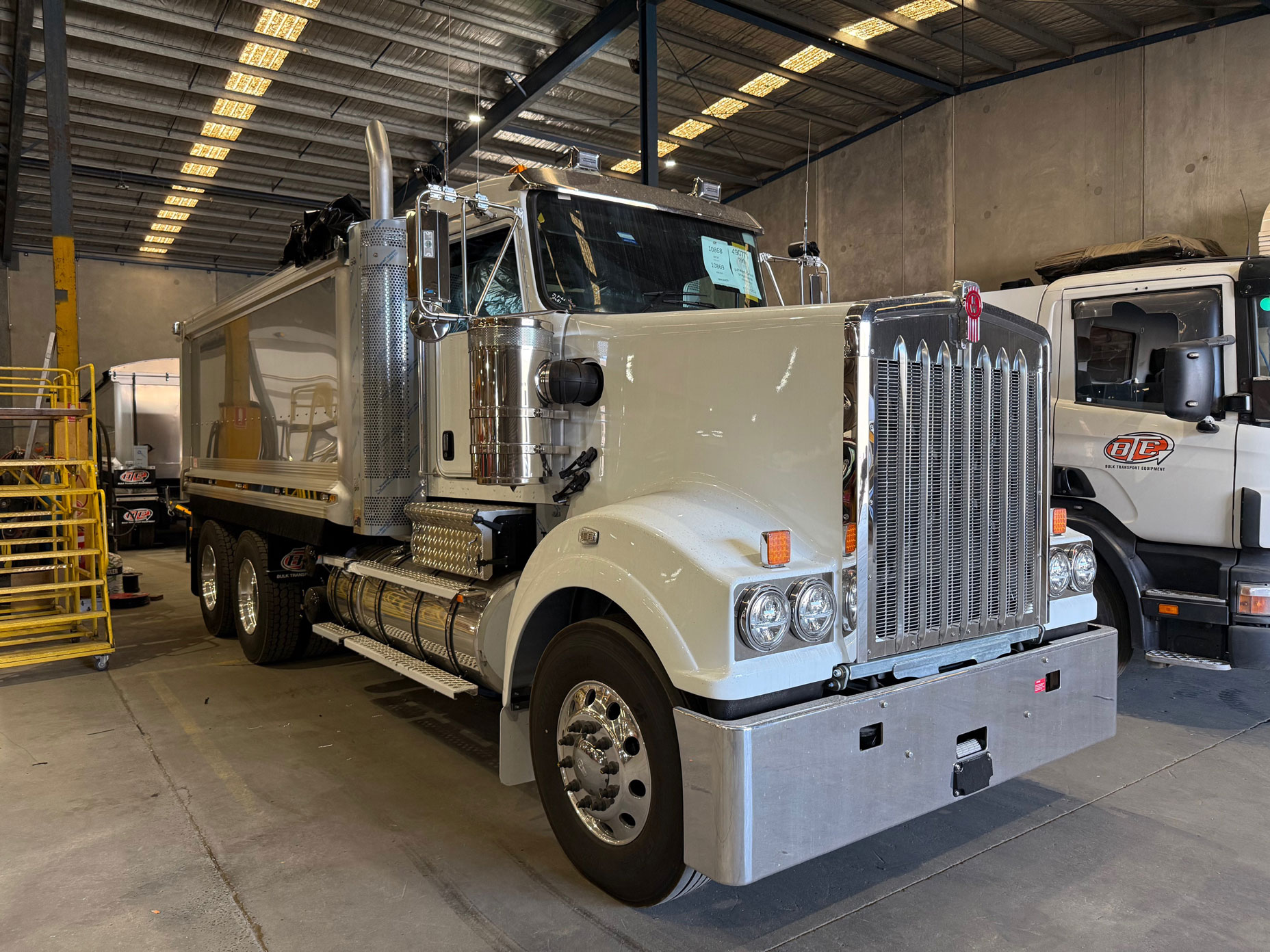
BTE – Bulk Transport Equipment
Challenges in Achieving J4 Compliance
The transition to the VSB6 J4 Tipper Code presents several challenges for tipper body manufacturers and builders. While the compliance changes aim to improve safety and standardisation, the certification process can create bottlenecks, redesign costs, and approval delays if not managed correctly.
Understanding What Needs to Change
One of the biggest concerns for manufacturers and AVEs is identifying which aspects of existing tipper body designs require modification to meet J4 compliance. Many tipper bodies currently in use were engineered under the J1 Code, meaning they were not assessed against the updated J4 structural and safety benchmarks.
For manufacturers, this means evaluating existing designs to determine where modifications are necessary while minimising costly redesigns and production disruptions.
For AVEs and other approved engineering signatories, it requires a thorough understanding of the new compliance criteria to accurately assess structural integrity and safety components when certifying vehicles.
Key design elements that now require assessment and potential updates include:
- Tipper hinge – ensuring proper strength, alignment, and durability under operational stress.
- Subframes and mounting to chassis – reinforcing structural connections to improve safety and compliance.
- Tailgate design and grain doors – ensuring secure closure, load containment, and improved safety mechanisms.
- Hoist cross members – enhancing lifting stability and reducing stress on structural components.
- Pneumatic and hydraulic layout – improving the efficiency and reliability of tipper body movement.
- Tipper control and warning systems – ensuring proper operator alerts, controls, and fail-safes to prevent unsafe tipping operations.
For manufacturers, this means assessing current tipper body designs and making targeted structural and mechanical adjustments to meet NHVR standards, while minimising costly redesigns and production disruptions.
For AVEs, this requires thorough evaluation of updated tipper body designs to ensure they meet J4 compliance criteria, providing manufacturers with clear certification pathways.
The Risk of Delayed Compliance
With the J4 compliance deadline fast approaching, there is no flexibility for extensions or exemptions. From 1 April 2025, all new tipper body designs must comply with the updated J4 standards, or they will not be permitted on the road.
At this stage, manufacturers and AVEs can no longer afford to delay compliance efforts. The phased implementation is already in motion, and any uncertainty or late action could lead to operational disruptions, certification bottlenecks, and compliance failures. Acting now ensures a smoother transition and avoids last-minute complications.
Key risks of delayed compliance include:
- Insufficient time for design adjustments, leading to rushed assessments, compliance failures, and costly rework.
- Limited availability of Approved J4-accredited Vehicle Examiners, increasing the risk of delays in certification and last-minute bottlenecks.
- Restricted time to source and implement necessary modifications, as supply chain constraints may make it harder to obtain compliant components before the deadline.
To avoid these risks, manufacturers should finalise compliance assessments and approvals now.
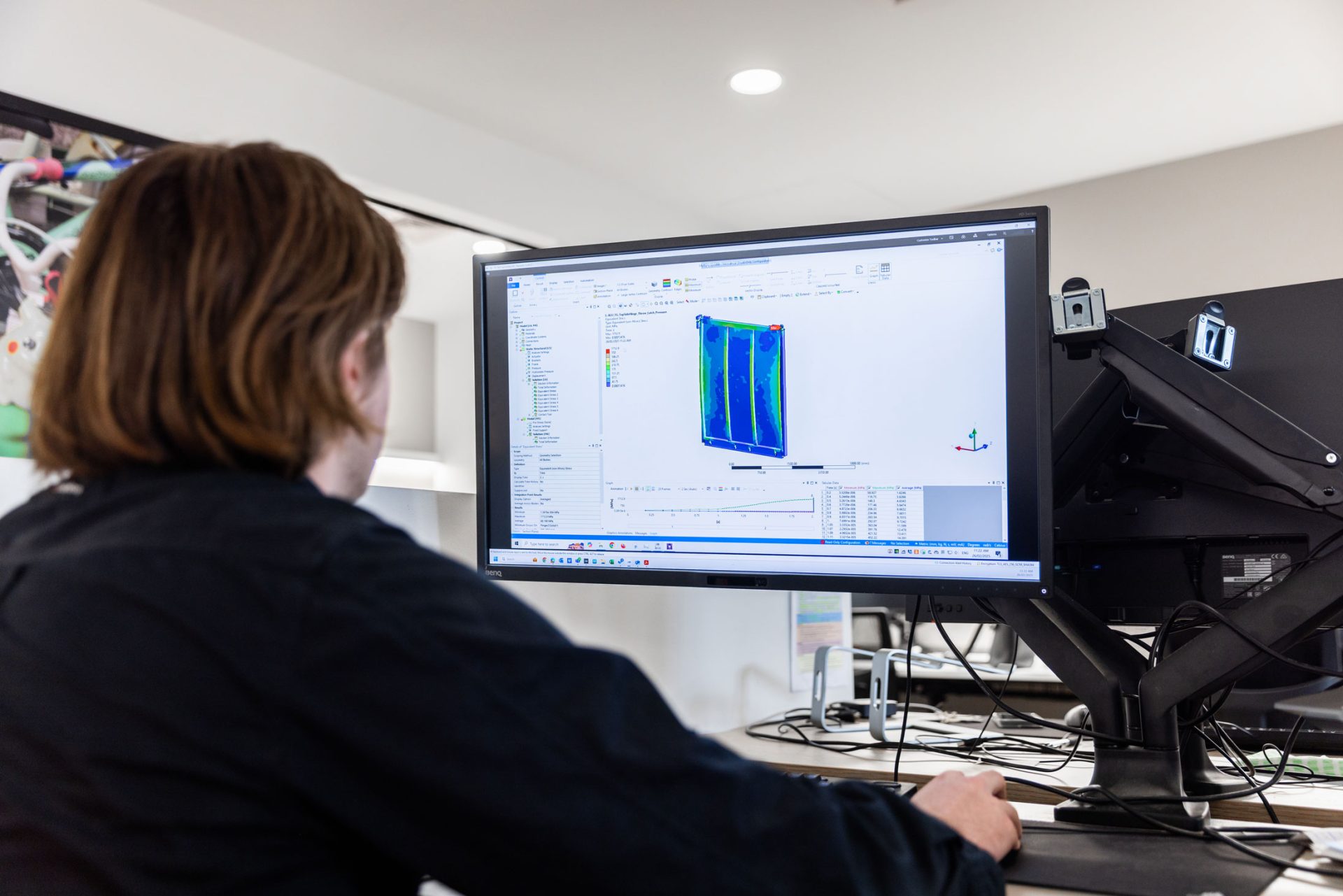
VSB6 Section J4
Balancing Compliance with Production Efficiency
For tipper body builders, compliance must be integrated into production workflows without causing delays or unnecessary design overhauls. The challenge is ensuring that J4 compliance is achieved without compromising manufacturing efficiency.
Common Concerns:
- Will we need to re-engineer our designs from scratch?
- Will compliance slow down production timelines?
- How much will modifications cost?
At Smedley’s, we minimise design changes wherever possible by:
- Assessing existing designs first to determine if they can meet J4 standards with minimal modifications.
- Providing comprehensive engineering reports that streamline the certification process with AVEs.
- Offering expert guidance on small but effective design adjustments, reducing rework and cost.
Ensuring Certification Readiness
Even if a manufacturer’s design is structurally sound, it still needs to be officially assessed and certified to meet J4 compliance. This process involves submitting detailed engineering reports, supporting drawings, and structural assessments for review by an AVE.
Common mistakes that cause delays:
- Incomplete documentation leading to assessment rejections.
- Lack of engineering analysis to prove compliance.
- Misalignment with AVE expectations, requiring resubmissions.
- Comprehensive compliance reporting – Smedley’s provides all necessary technical documentation to meet J4 certification standards.
- Pre-assessment reviews – We conduct internal design checks before AVE submission to prevent rejections.
- Direct AVE collaboration – Our team works closely with AVEs to ensure a seamless approval process.
How Smedley’s Engineers Simplify J4 Compliance
Transitioning to the VSB6 J4 Tipper Code doesn’t have to be a complicated or disruptive process. At Smedley’s Engineers, we specialise in minimising compliance challenges by using a structured, engineering-led approach. Our goal is to help manufacturers and AVEs achieve J4 certification efficiently – without unnecessary redesigns or production delays.
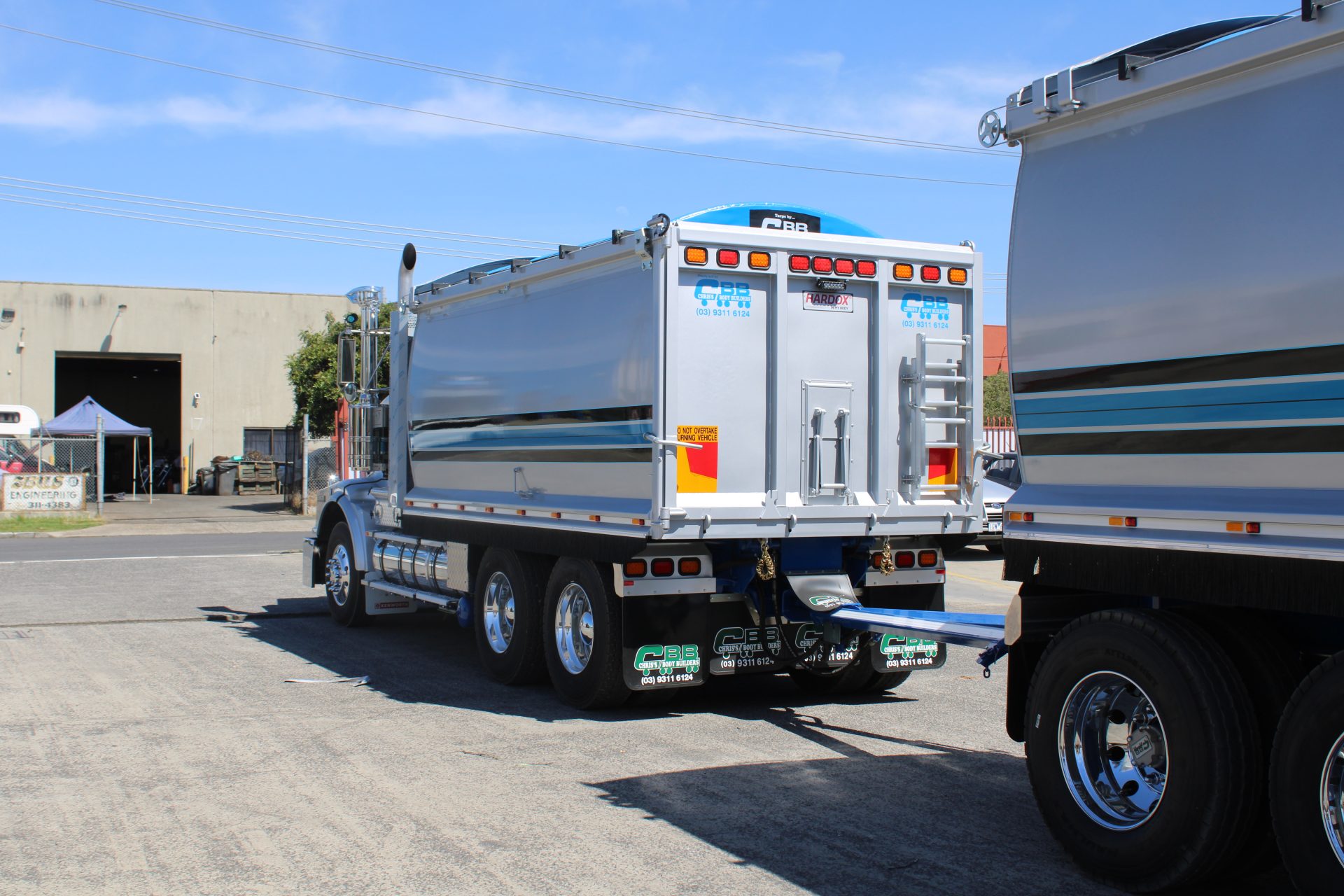
Chris’s Body Builders
Here’s how we make J4 compliance seamless:
Engineering Expertise Backed by Real-World Data
Many compliance consultants simply review documentation and flag potential issues, but Smedley’s goes further by conducting in-depth engineering assessments.
Finite Element Analysis (FEA) Modelling
We use FEA simulations to test chassis stress points, tipper hinge durability, and overall structural integrity – ensuring that existing designs can comply with J4 without major changes.
Real-World Load Testing Insights
Our engineers don’t just rely on theoretical data – we use real-world failure analysis and past compliance cases to guide practical J4 assessments.
A Holistic Approach to Heavy Vehicle Compliance
Unlike firms that focus solely on one aspect of compliance, Smedley’s offers:
- Full vehicle design & engineering support
- Manufacturing drawings for J4-certified designs
- ADR compliance & homologation testing
By leveraging our deep industry experience, we help manufacturers validate and optimise their designs without overhauling them unnecessarily.
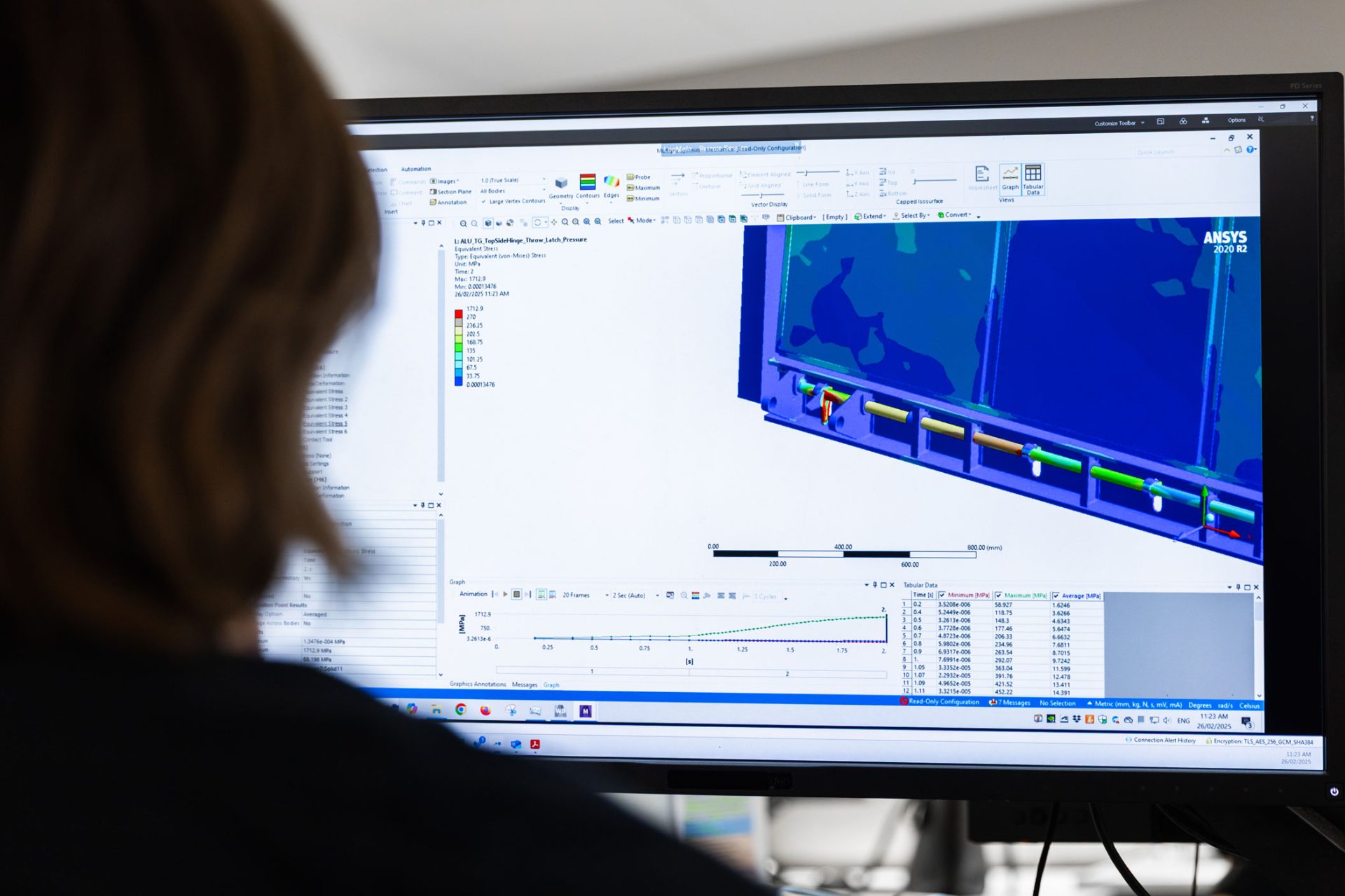
VSB6 Section J4
Minimising Disruptions to Existing Designs
One of the biggest concerns for manufacturers is the fear that J4 compliance will require costly and time-consuming design overhauls.
The Reality? Most existing tipper body designs do not fail compliance outright – they just need proper assessment and minor refinements.
- Instead of making designs fit a rigid compliance report, we assess what already works and adjust where necessary.
- We capture a broad range of assessments to allow for small design variations, preventing the need for multiple approvals.
- Our method ensures minimal downtime so manufacturers can continue production while securing compliance.
A Clear, Step-by-Step Compliance Process
We take the complexity out of J4 certification by following a structured, transparent process that ensures manufacturers know exactly what to expect.
Step 1: Initial Consultation
- A phone call to understand the manufacturer’s current designs and J4 readiness.
- Identifying potential compliance gaps and necessary engineering assessments.
Step 2: Structural Assessment
- Conducting FEA modelling & hand calculations to assess tipper hinge strength, chassis stress points, and compliance factors.
- Reviewing existing designs to see where minimal changes can be made for compliance.
Step 3: Compliance Reporting
- Providing detailed engineering reports that meet NHVR & AVE requirements.
- Supporting documentation with 3D CAD designs & analysis results.
Step 4: Certification & AVE Liaison
- Direct collaboration with AVEs to streamline the approval process.
- Assisting manufacturers in submitting the required documents for official certification.
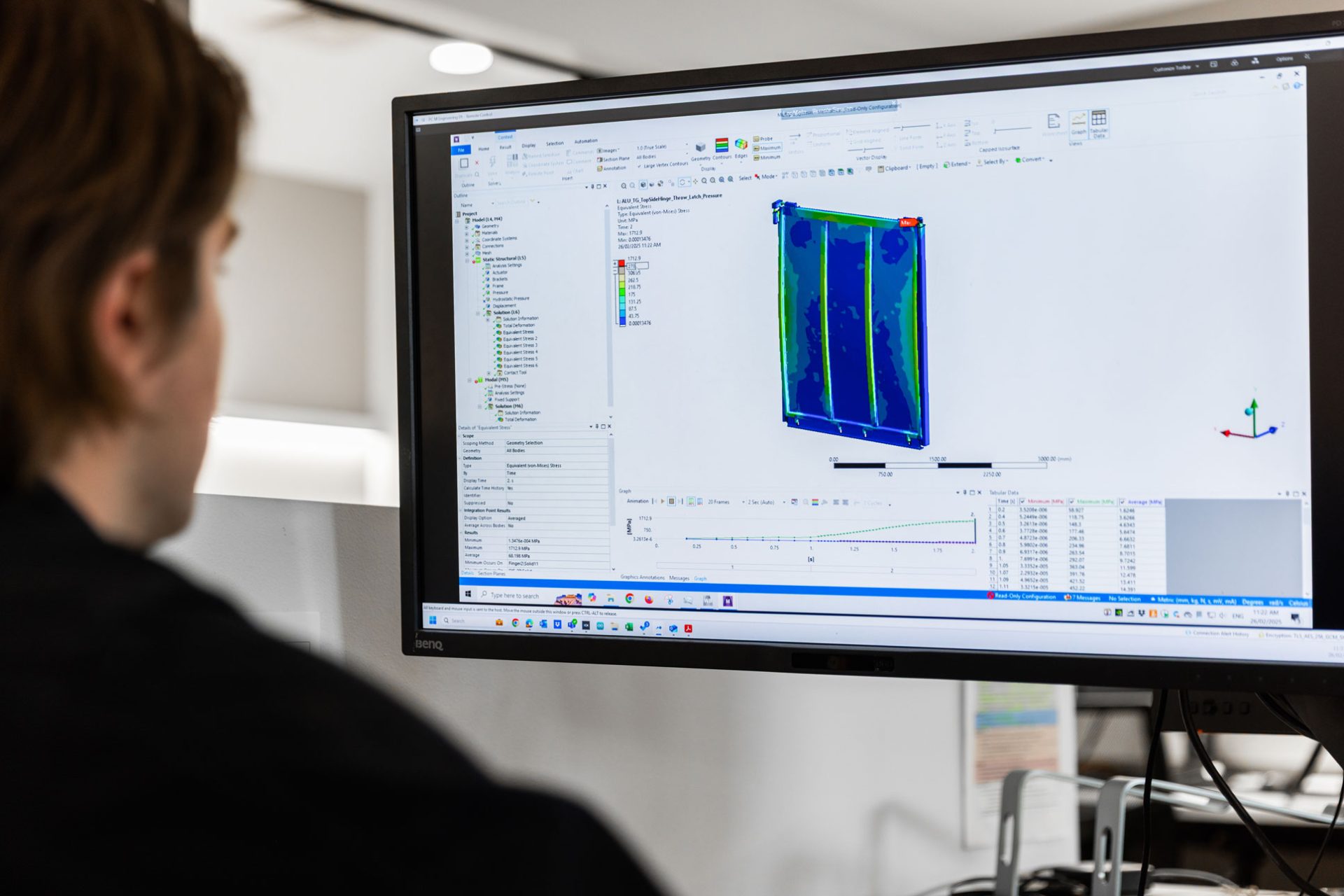
VSB6 Section J4
Why Choose Smedley’s Engineers?
With the VSB6 J4 Tipper Code deadline fast approaching, manufacturers and AVEs need a trusted compliance partner who can navigate the complexities of certification without unnecessary delays or costly redesigns.
Smedley’s Engineers stands out as a leader in tipper body compliance, offering a streamlined approach that ensures manufacturers and AVEs achieve J4 certification efficiently and with minimal disruption.
A Full Suite of Engineering Services Under One Roof
Unlike many compliance providers that only focus on individual aspects of certification, Smedley’s Engineers offers a complete, end-to-end service. Our team handles everything from tipper body compliance assessments and structural engineering analysis to full vehicle design, manufacturing drawings, and ADR compliance testing. This means manufacturers don’t need to juggle multiple consultants – Smedley’s Engineers provides all the necessary technical expertise in one place.
Beyond certification, our engineering services extend to failure analysis, homologation testing, and expert witness support, making us one of the most comprehensive heavy vehicle compliance teams in Australia. Our approach saves manufacturers time and resources by ensuring the entire compliance journey is managed efficiently and with expert precision.
Industry Experts with a Deep Understanding of Compliance
At Smedley’s Engineers, compliance isn’t just about ticking boxes – it’s about ensuring manufacturers can meet regulatory requirements without disrupting production or redesigning their entire fleet. Our team has decades of experience in heavy vehicle engineering, with specialists dedicated exclusively to NHVR and VSB6 compliance.
With in-house access to FEA modelling, CAD design, and structural testing tools, we provide highly detailed assessments that eliminate guesswork. Our strong industry relationships, including direct collaboration with AVEs, allow us to fast-track approvals and streamline the certification process. We know exactly what AVEs look for in J4 compliance assessments, ensuring our reports meet the highest industry standards the first time around.
Achieving Compliance Without Unnecessary Design Changes
One of the biggest concerns manufacturers face is whether J4 compliance will require major design overhauls. In reality, most existing tipper body designs do not need to be significantly altered – they just need to be properly assessed.
Our approach prioritises minimising changes while maximising compliance efficiency. Rather than forcing manufacturers to completely re-engineer their designs, we first assess the existing structure to determine what already meets J4 requirements. When modifications are needed, we identify the simplest and most cost-effective adjustments, ensuring manufacturers can maintain their existing workflows without production delays or excessive costs
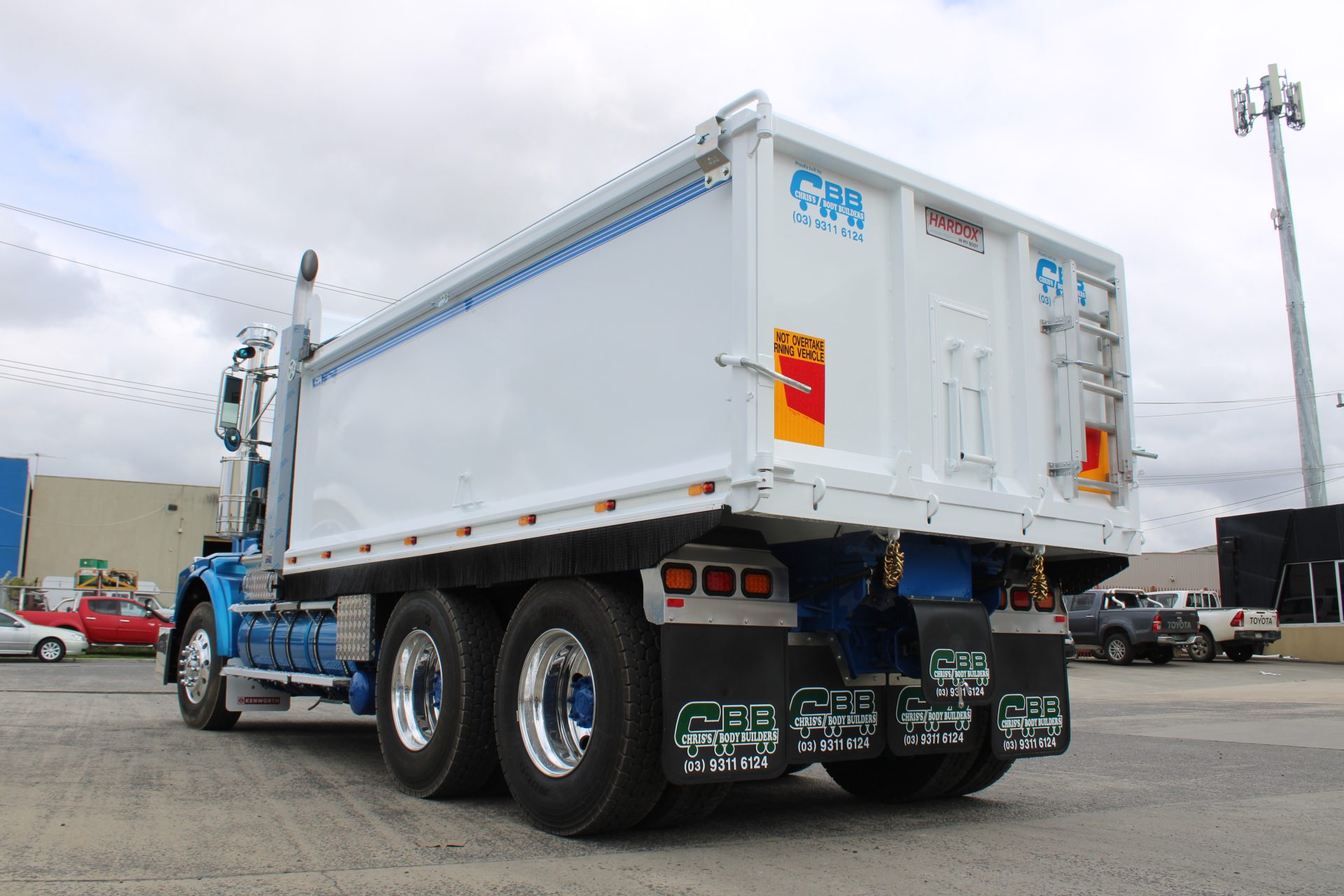
Chris’s Body Builders
A Proven Track Record in Heavy Vehicle Compliance
Smedley’s Engineers has worked with tipper manufacturers and AVEs across Australia, delivering successful compliance solutions for a wide range of heavy vehicle applications. We have helped manufacturers meet previous VSB6 requirements for drawbars and towbars, conducted chassis stress analysis for tipper builders, and provided FEA testing for heavy vehicle components.
Our real-world experience in design validation and certification means we understand the challenges manufacturers face and have the technical expertise to solve them. By partnering with Smedley’s Engineers, manufacturers gain access to an experienced team that knows how to navigate J4 compliance efficiently and effectively.
How to Get Started with VSB6 J4 Tipper Code Compliance
With the VSB6 J4 Tipper Code deadline fast approaching, manufacturers and AVEs must take action now to ensure compliance before the 1 April 2025 enforcement date. Delaying the process increases the risk of production disruptions, last-minute assessment bottlenecks, and potential non-compliance issues.
At Smedley’s Engineers, we make the transition to J4 compliance as smooth and efficient as possible. Whether you need a full assessment of your existing designs, engineering validation, or certification-ready documentation, our team is here to help.
Secure Your VSB6 J4 Tipper Code Compliance Today
The clock is ticking on J4 implementation, and waiting too long could mean not having enough time to fine-tune designs to meet the requirements. Manufacturers and AVEs who act now can avoid last-minute compliance issues and ensure their designs are certified well before the deadline.
📞 Contact Smedley’s Engineers today to schedule your initial consultation. Our expert team is ready to guide you through the process and provide the technical support you need to meet J4 standards with confidence.
For full details on the compliance timeline, visit the NHVR website.
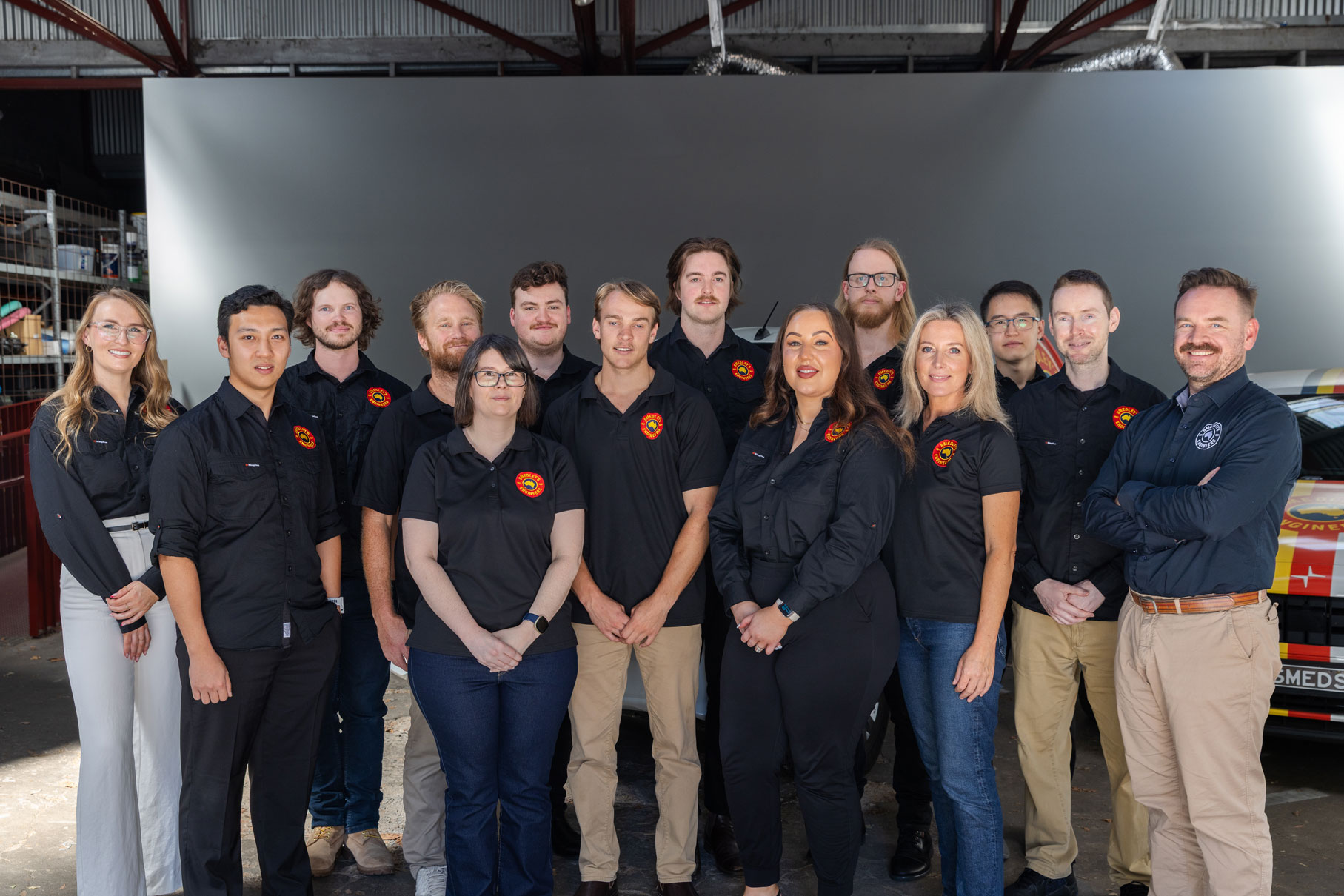
Smedley’s Engineers
Glossary of Terms
Approved Vehicle Examiner (AVE) – A qualified professional authorised to assess and certify heavy vehicle modifications for compliance with VSB6 and other NHVR regulations. AVEs may be referred to differently in various states and territories:
- QLD: Approved Person (AP)
- NSW: Licensed Certifier
- VIC: Vehicle Assessment Signatory Scheme (VASS) Signatory
- SA: Recognised Engineering Signatory
- WA: Chartered Professional Engineer (CPEng) or Vehicle Examiner
- TAS: Engineering Signatory
- NT: MVR-Approved Engineer
- ACT: Road Transport Authority (RTA) Approved Engineer
Finite Element Analysis (FEA) – A computational method used to predict how structures will react to forces, vibration, and other physical effects, ensuring compliance with J4 structural requirements.
Homologation – The process of certifying that a vehicle or component complies with all relevant regulations and standards before being registered or put into service.
J4 Tipper Code – A section of the NHVR’s Vehicle Standards Bulletin 6 (VSB6) that establishes compliance requirements for tipping body fitments on heavy vehicles, effective 1 April 2025.
National Heavy Vehicle Regulator (NHVR) – The regulatory authority responsible for overseeing heavy vehicle compliance, safety, and standards across Australia.
Structural Assessment – A technical evaluation of a vehicle’s structural components (such as tipper hinges, subframes, and hoist cross members) to ensure they meet durability and safety standards.
VSB6 (Vehicle Standards Bulletin 6) – The official guide outlining modification requirements for heavy vehicles in Australia, ensuring modifications meet safety and compliance regulations.